WHY GLOBAL MANUFACTURERS SHOULD TAKE A PHASED APPROACH TO FLEET ELECTRIFICATION
April 23, 2020
XING MOBILITY - OPINION PIECE
According to industry experts in a large number of recent reports, electrification is well-underway in commercial and industrial markets. However, there remain significant delays in adoption, partially stemming from capital investment and the perceived risk associated with brand new technologies. In addition, many manufacturers have sizable commitments tied up in existing designs and tooling, and vehicle makers in specialty markets are significantly undeserved when it comes to easily adaptable, production-ready electrification solutions. In order to mitigate these concerns, XING Mobility is striving to offer customers the option of gradual investment and adoption by employing highly modularized technology and encouraging phased approaches to electrification. We’ve put together some insights on how a phased adoption program can benefit your plans for electrifying vehicle fleets:
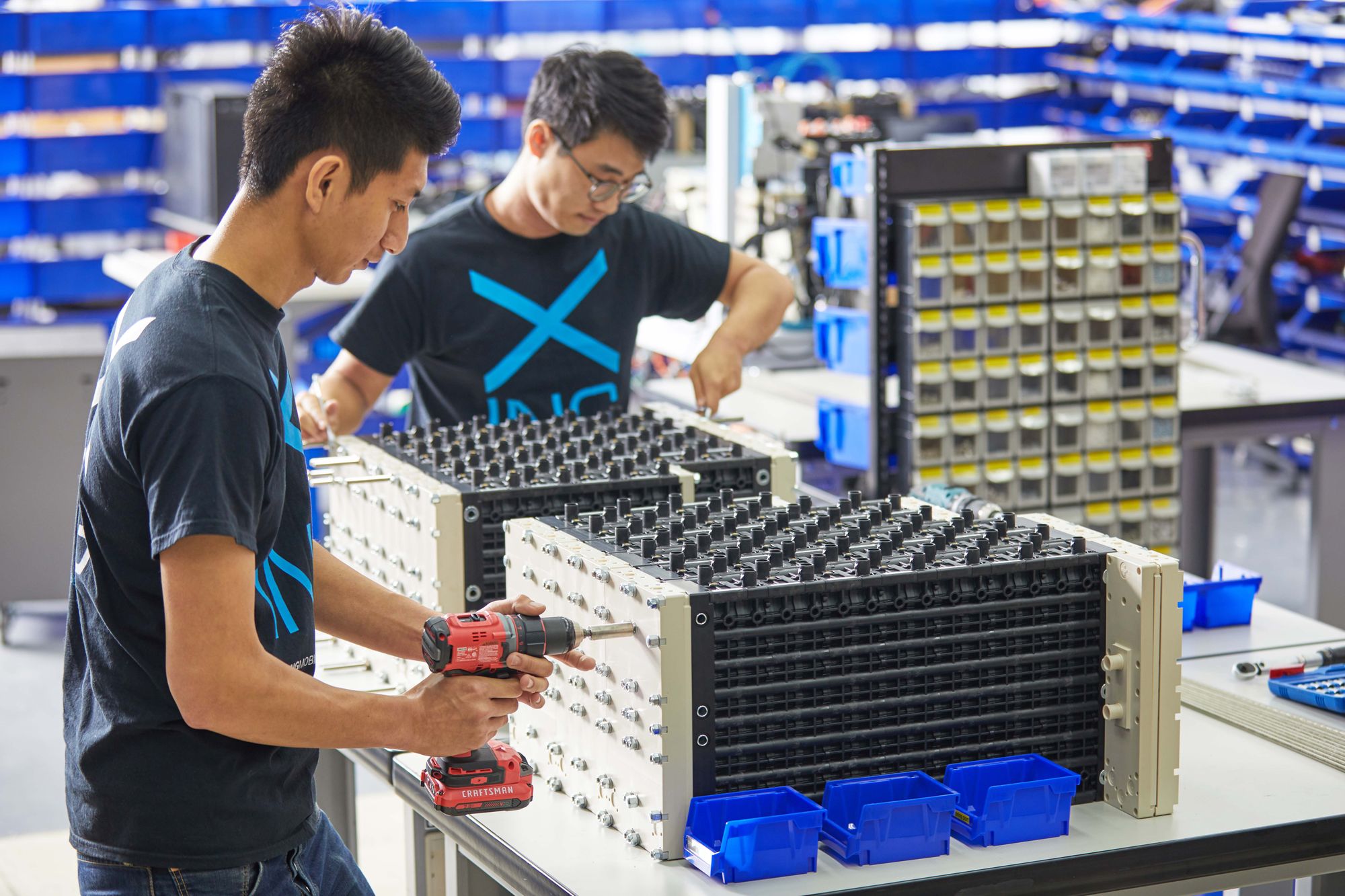
A journey from standard parts to fully customized solutions
Understanding that large scale R&D and tooling resources may not be available to all vehicle and equipment manufacturers, XING Mobility has worked to develop solutions and capabilities to serve customers at every stage of electrification. In our extensive experience of serving small-medium sized vehicle makers, we have distinguished 3 key phases in the advancement of a manufacturer's EV program: 1) prototype development 2) validation & testing and 3) mass production.
While latter stages of mass production (and delivering newly electrified equipment to the market) often require a higher level of customization and investment to ensure the greatest level of efficiency and specialization for each and every vehicle type, the early stages of development and testing can benefit from standard, modularized parts that require little if any customization or upfront capital. By using less capital intensive solutions earlier in the development program, manufacturers can accelerate integration work and testing phases without taking on huge investment commitments.
Phase 1: Prototype Development
XING Mobility has recognized that when developing an electric prototype, the priority for many of our customers is getting testing underway as soon as possible. As a result, our company has developed IMMERSIO™ Battery Pack System™, a highly modular, pioneering battery solution designed to achieve the best compromise between performance, efficiency, cost, and speed of install. With its shape and size measuring 30 x 7 x 8 cm and weighing just 2.8 kg, this advanced lithium-ion battery module makes for an ideal building block as an initial power source for prototypes, stacking to fit to a wide range of vehicle types. This feature also allows vehicle manufacturers to easily and quickly convert vehicle fleets and to utilize existing or unused chassis as the compact size and flexibility of the module can accommodate unusual geometry or packaging dimensions.
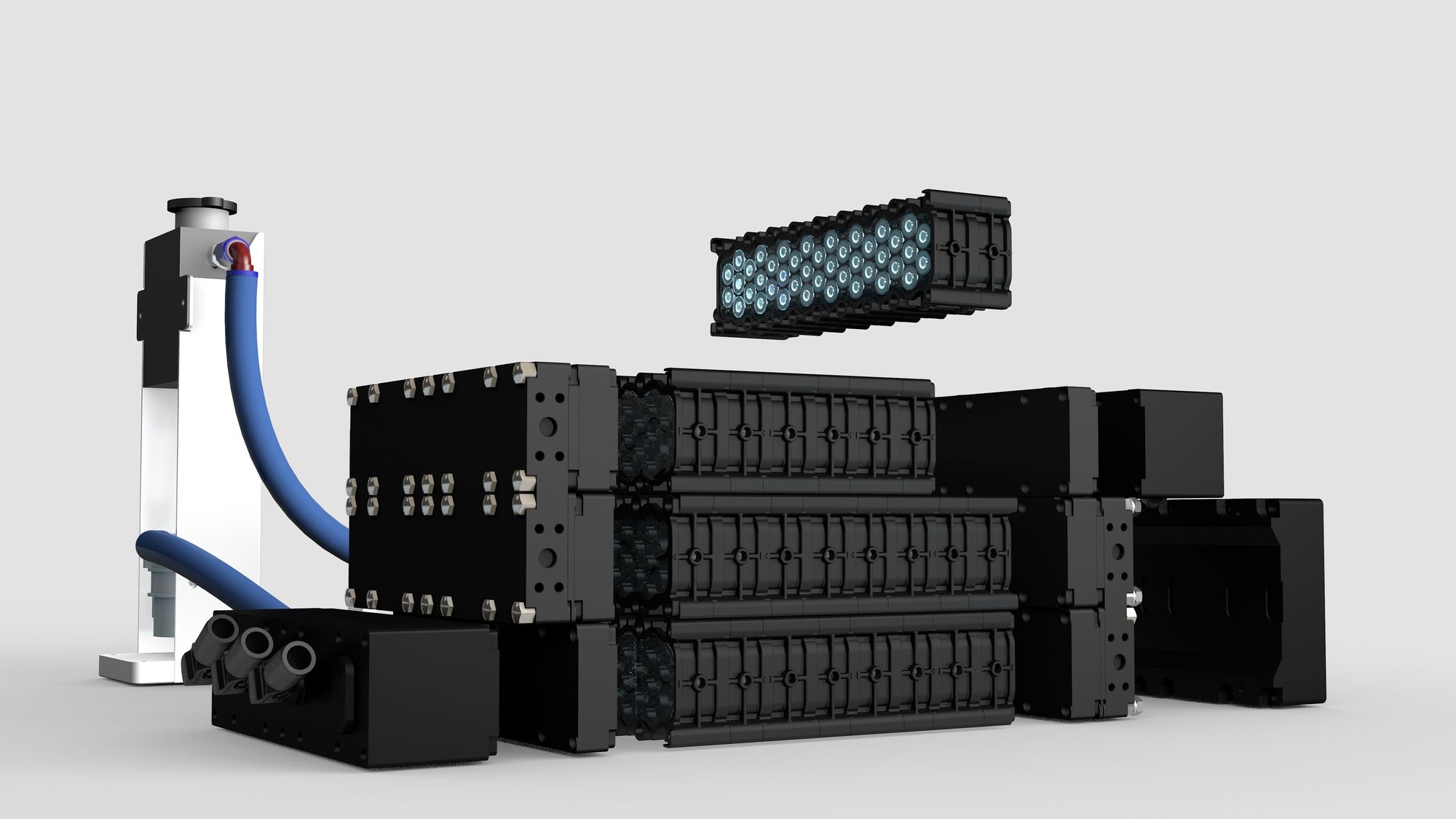
Phase 2: Validation & Testing
While XING Mobility's standard modules can often be more than sufficient for the purposes of validation, testing and homologation, some vehicle makers will want to opt for semi-custom solutions. Using technology already tested and proven in the IMMERSIO™ Battery Pack System™, semi-customized variations of this module can allow for more precise data to be collected for a particular application on vehicle type. For example, some customers may decide to work with our advanced engineering consulting team to adjust the dimension, cell-type or shape of the module to be more compatible with their series production aims, without needing to incur the development cost of a fully unique system. In doing so, this medium-cost solution serves to further stretch out the capital investment required to develop EVs.
Phase 3: Mass Production
Ultimately, for many manufacturers, the end goal will be to develop fully-customized, data-derived battery packs that are tailored to a particular application down the last centimeter or kilowatt hour. This may involve a total clean sheet design, and as a total solution provider XING Mobility has worked with customers in a range of industries to innovate brand new, energy-dense, entirely specialized systems that achieve the greatest efficiency for a particular vehicle or equipment function. In addition to selecting and designing the right cell type, enclosure materials and cooling method, we work closely with our customers to analyze and develop series production methods, molds and assembly lines.
Our takeaway
In spreading the cost of development and weighting custom tooling and capital investment towards the mass production phases, original equipment manufacturers (OEMs) can rapidly grow accustomed with all-electric or hybrid-electric technology and avoid being left behind competitors who already have E-Mobility programs underway. In particular, this approach could be particularly beneficial in the construction, mining and agricultural sectors where many vehicle makers specialize in low-volume, high-mix applications and the cost of developing unique systems for each and every application can be extremely costly and time intensive.
If you are interested in learning more about XING Mobility’s high performance energy storage and powertrain systems, please contact us at: sales@xingmobility.com